Form Grinding, Explained
When it comes to precision grinding, there are so many specific types of processes that it can be difficult to fully comprehend the seemingly endless number of them. Every grinding process brings with a certain complexity, so they each require a thorough understanding and a skilled hand to yield the best results. One process which is difficult to explain is form grinding, which is exactly what we endeavor to accomplish today. What is form grinding, how does it work, and how can it be beneficial to aerospace manufacturers? Let's discuss.
Click Here for our Ten Facts About Centerless Grinding Infographic
Form Grinding, sometimes called non-generating grinding, is a specialized type of cylindrical grinding where the grinding wheel is the exact shape of the final product. A specialized form is added to the face of a grinding wheel and then imparted onto the workpiece during grinding. In this technique, a disc wheel is used to grind both sides of the space between splines simultaneously. An involute form is attached to the wheel to help guide the process.
When it comes to gear grinding, a form grinder is capable of working both external and internal spur and helical gears up to 36" in diameter. An automatic grinding cycle is provided which reduces the reliance on operator skill while also increasing the accuracy of the gears ground on a production basis by ensuring exact repeatability of the selected cycle.
A form grinder is capable of working both external and internal spur and helical gears.
The automatic grinding cycle reduces the hazard of surface tempering. However, additional insurance can be had and better finishes obtained by using a high-grade, well-filtered, grinding oil.
Let's look at some of the benefits of using form grinding wheels for your aerospace projects:
-
Accurate control of form
-
Maintain any modified profiles
-
Possible to grind finer forms from the solid where heat treatment allows
-
Non-standard forms can be ground
-
Capable of grinding full-form
-
No dressing is required
-
Free cutting without heat checking
-
More economical
-
Long life
-
Reduced grinding time
-
Low machine wear
-
High precision
For best results, the grinding wheels most recommended for this process are vitrified aluminum oxide wheels with 29A semi-friable or universal 38A abrasive. The grain sizes may vary from 46 to 80 for combined rough and finish grind.
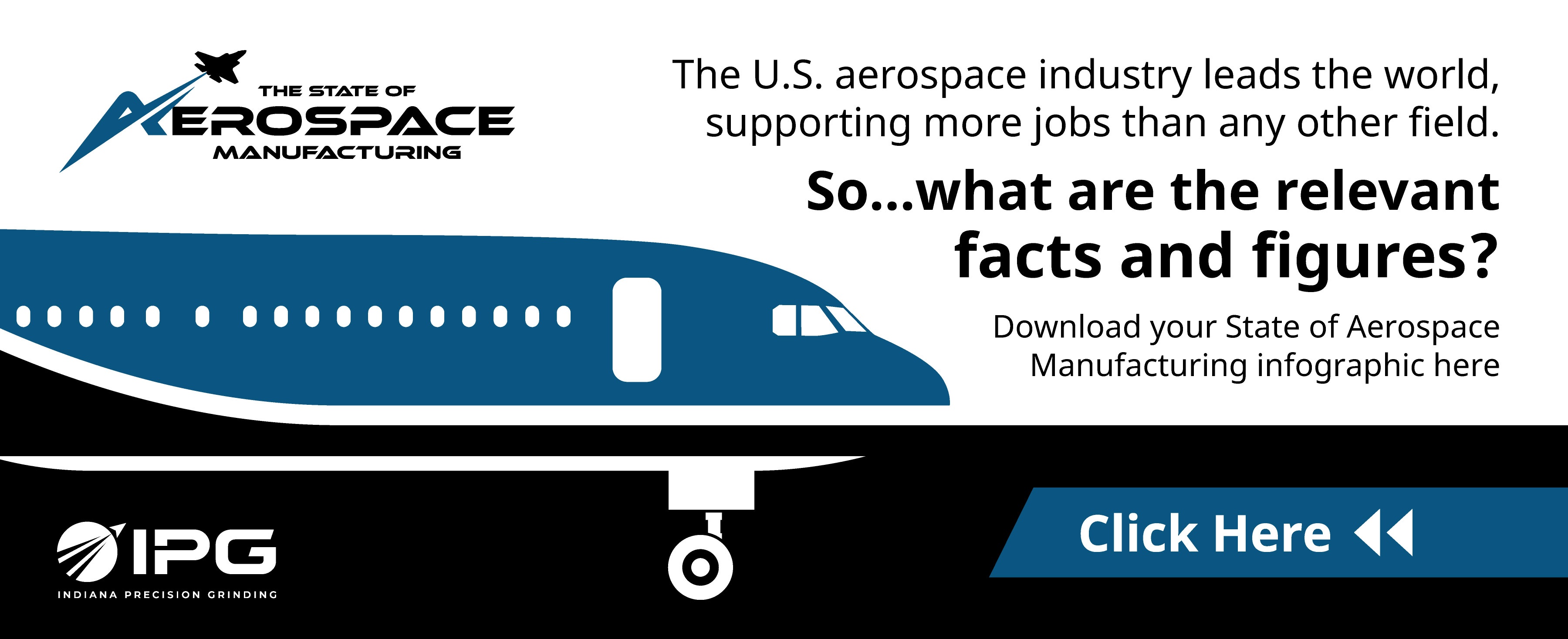